
CORED WIRE
Cored wire is fabricated into a tubular wire with a calculated mixture of alloys uniquely blended together; such as CaSi, Carbon, etc.
The blended mixture is then metered into the wire during the fabrication process, producing special alloy cored or flux cored wire in various diameters, depending on customers’ requirements and needs.
ADVANTAGES OF CORED WIRES
​
1. Wire feeding technology can make fine adjustments to the chemistry of metal. Wire feeding technology can also Increase alloy element's recycling rate.
2. The steel liquid treated by wire feeding technology is stable and well-mixed, Secondary oxidation will be avoided. The mixture will speed up to float. The steel liquid will be clear and well mixed.
3. Wire feeding can prevent air being brought into the steel liquid.
4. Wire feeding technology has good adaptability, needs small investment, and has a good application range.
5. Wire feeding technology needs simple facilities, simple operations, and is environmentally friendly.

1- Ca-Fe Cored Wire
The calcium iron cored wire functions as the deoxidizer and the desulfurizer in the process of steel-smelting production, mainly applied to cold heading steel, pipe line steel, and other low-silicon steel types. Its core power material is metal calcium and pure iron powder. Its deoxidized outcome – CaO is also mingled and combined with Al2O3 system in the liquid steel to generate 7 Al2O3.12CaO sinter of low-melting point, thus to avoid the effect of nozzle blockage arising from condensation of casting nozzle mingled with Al2O3 system, so as to ensure a smooth continuous casting production. The desulfurized outcome floats upwards very easily to be removed, so as to enhance the plasticity and tenacity of steel.


2- Ca-Si Cored Wire
Casi cored wire is the ideal deoxidizer of refining special steel and alloy steel, also is the reductant of producing core technology is the rise in recent years as a means of refining furnace is widely used in modern practice of steel wire feeding technology. Alloy cored wire can used to purity the liquid steel to practice, to change inclusion morphology properties of the alloy, can significantly improve the recovery rate,reduce training costs of steel, its. Economic effect is remarkable.
The active element in CaSi is calcium. For aluminum-silicon-killed steels, Calcium treatment by CaSi is normally cheaper than by pure Calcium products. For the molten steel, calcium treatment is a must.
Calcium is used to transform alumina into low melting point calcium-aluminates, avoiding nozzle clogging as well as to control the shape of oxide and sulfide inclusions. During the course of deoxidation and inclusion transformation, efficient calcium treatment plays a very critical role.
With advantages as below:
Eliminate alumina nozzle clogging, spheroidize oxide and sulphide inclusions which increases the tranverse toughness and strength of steel. Improve steel purity.

3- Fe-Ti Cored Wire
Titanium at steel-making temperatures forms very stable compounds with oxygen, carbon, nitrogen and sulphur. Because of this property, it is often used in steel-making to fix these elements, neutralizing their harmful effects.
4- C Cored Wire
Carbon plays very important role for keeping the steel physical and chemical properties. It is mainly for keeping the steel strength. In reverse, Carbon adding reduces the steel toughness and weldability. Carbon content in the steel after smelting and refining is required to maintain around certain value. Feed Carbon cored wire can reach the final carbon content required by the steel. Carbon has low density and it is easy to suspend on the steel slag surface and thus burning waste happens. Carbon cored wire can be fed to the ladle bottom to avoid material waste and it can be dissolved in steel quickly and uniformly. The cored wire can also be used for components minor adjustment of low carbon steel.
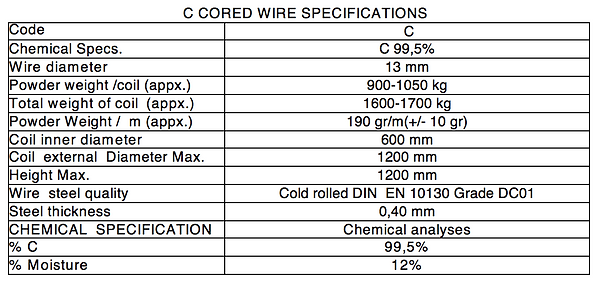
5- S Cored Wire
Sulfur is considered as a kind of harmful impurity and it is controlled as low as possible while steel-making.
Although sulfur has some negative effects, it is often used to improve the machinability of steel and it can also reduce the tool wear.
The solubility of sulfur in the steel is relatively low. The main purpose of sulfur in the liquid steel is the formation of a particular ingredient or complex inclusions to improve the steel machinability. Sulfur is usually added to the liquid steel in the form of pure sulfur, iron sulfur or pyrite. Because the density and boiling point of sulfur is pretty low, feeding sulfur wire is a kind of effective way to add the sulfur.


6- Ca Cored Wire
The pure calcium cored wire is mainly used for Al-killed steel.
Due to its low density, low boiling point and high oxidability, calcium needs to be released near the ladle bottom in order to have the best recovery.
Calcium is used to transform alumina into low melting point calcium-aluminates, avoiding nozzle clogging as well as to control the shape of oxide and sulfide inclusions.
​
The advantages as below:​
Eliminate alumina nozzle clogging, spheroidize oxide and sulphide inclusions which increases the transverse toughness and strength of steel. Improve steel purity. Avoid silicon addition.
