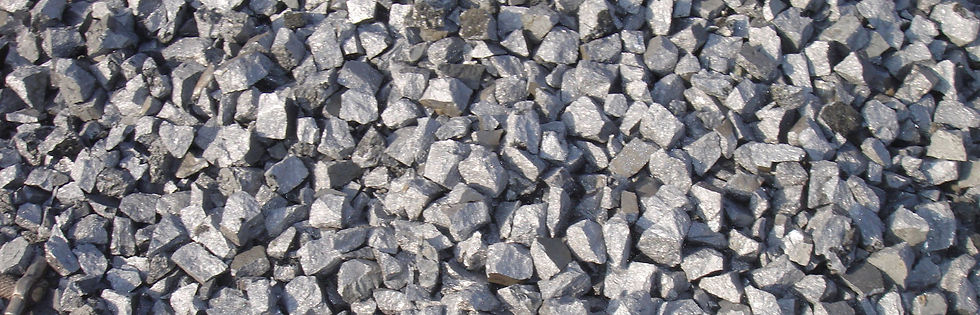
FERRO-ALLOYS
FERRO-CHROME
Properties of Ferrochrome
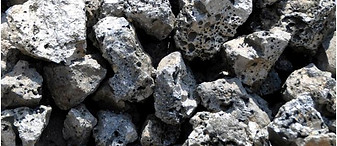
Over 80% of the world's Ferro-chrome is used in the production of stainless steel, which is defined as a steel alloy with a minimum of 10% chrome by content, the average chrome content being 18%. Stainless steel depends on chrome for its appearance and its corrosion-resisting properties.
High Carbon Ferro-Chrome is most commonly used in specialist applications such as engineering steels. Lower carbon Ferro-chromes are produced in smaller quantities for more specialized applications.
Production of Ferro-chrome
The two main products of chromite refining are Ferro-chrome and Chrome Metal. For the production of Ferro-chrome, the chromite ore is reduced, usually by coal and coke in a high-temperature reaction to form the iron-chrome alloy. For the production of pure chrome, the iron has to be separated from the chrome in a two-step roasting and leaching process. Over 80% of the world's Ferro-chrome is utilized in the production of stainless steel, which is defined as a steel alloy with a minimum of 10% chrome by content, the average chrome content being 18%. Stainless steel depends on chrome for its appearance and its corrosion resisting properties
Ferro-chrome is often classified by the ratio of chrome to carbon it contains. The vast majority of ferro-chrome produced is Charge Chrome. It has a lower Cr:C ratio and is most commonly produced in South Africa for use in stainless steel production. The second-largest segment of the market is High Carbon Ferro-chrome which has a higher chrome content, being produced from higher grade chrome ore.
​
High Carbon Ferro-chrome​
With a chrome content from 60% minimum, there are several variations on High Carbon Ferro-chrome with carbon contents of:
Cr : 60 %
Si : 3 - 3.5% Max
P : 0.35% Max
S : 0.35% Max
C : 6 - 8 %
​
Low Carbon Ferro-chrome​
Low Carbon Ferro-chrome is produced by reducing chrome ore with Ferrosiliconchromium, typically the chrome contents are minimum 60% with carbon contents ranging from 0.03% to 0.15% sometimes higher depending on the origin. It is used for trimming additions in stainless steel production as well as other specialist applications. It is added by stainless steel producers in the last stages of production to add precise amounts of chrome without affecting the carbon levels. An intermediate-carbon Ferro-chrome is produced by further refining of Charge Chrome by blowing oxygen and steam through hot molten Charge Chrome to reduce the silicon and carbon levels. Typically the carbon is reduced to below 1.5%.
Cr : 60 %
Si : 1.5% Max
P : 0.35% Max
S : 0.35% Max
C : 0.03%
FERRO-SILICON
Ferro-silicon is an atomized alloy, which is formed by combining iron and silicon with a silicon content range of 15% to 90%. Ferro-silicon is a universal "heat blocker" used in the production of carbon and stainless steel. This additive is used with other ferroalloys in the deoxidizing process of steel, as well as in the production of silicon itself. Ferro-silicon is used in the production of cast iron, as Ferro-silicon can accelerate graphitization. Ferrosilicon replaces the need for ferro-manganese, spiegeleisen and calcium silicides in the manufacturing process.
Standard Material
​
Si : 70 - 75%
Al : 1.5 % Max
C : 0.100%
P : 0.035%
S : 0.035%
Production of Ferrosilicon:​
A large portion of the global Ferro-silicon supply is manufactured in China, the USA and India. The most basic definition of the Ferro-silicon production process would be that the silica (or sand) is mixed with coke, and then a reduction process takes place in the presence of mill scale, scrap or another source of iron. A blast furnace is employed for Ferro-silicon production, but for larger contents of silica, an electric arc furnace is used. Ferro-silicon is usually supplied in bags of particles in pallet boxes or shrink-wrapped on pallets or in steel drums (50kg and dual-layer plastic bags or 1000kg packed in drums). The granularity of particles varies from 10 mm to 100mm.
​
Uses of Ferrosilicon:​
There are many practical applications of Ferro-silicon to include carbon steel and stainless steel production, and when using the Pigeon process to produce magnesium from dolomite. Applications in the production of other alloys include the manufacture of silicon steel for electro motors and cores, as well as coatings used during arc welding. One useful by-product of the production processes is silica fume, which is later added to concrete mixes to improve compressive and bonding strength there.​
​
Properties of Ferrosilicon:
Ferro-silicon has a melting point of 1200°C to 1250°C with a boiling point of 2355°C and Ferro-silicon contains about 2% of calcium and aluminum. Ferro-silicon, as an additive to the production process of ferrous metals, will impart several desirable properties upon the resultant alloy. Some of the primary benefits of adding Ferro-silicon to an alloy are to improve the corrosion-resistant properties of the new compound, as well as to add to the high-temperature heat-resistance properties of the new alloy, for example, in the production of silicon steel for use in transformer cores.
FERRO-MANGANESE

High Carbon Ferromanganese:
Ferro-manganese is produced by reduction of Manganese Oxide in blast furnaces or electric furnaces. It is a very flexible process in that the slags can be reprocessed into Ferro-silicomanganese which in turn can be further refined into Medium and Low Carbon Ferro-manganese. Ferro-manganese was invented in 1860 by Sir Henry Bessemer as a way to add Manganese during steel making with the advantage that a combination of Iron and Manganese Oxide results in a lower melting point for the alloy Ferro-manganese compared to pure Manganese Oxide. Standard Ferro-manganese (or High Carbon Ferro-manganese) is a commonly used alloy produced by the reduction of manganese ore in the presence of carbon. Typically it contains 75% manganese and 7% carbon. Worldwide production of Ferro-manganese in 2008 was approximately 4.5 million tons, with China being the worlds largest producer.
Low Carbon Ferro-manganese:
When liquid Silicomanganese is reacted with Manganese Ore or a high MnO rich slag, the silicon is oxidized increasing the Mn content of the alloy without an increase in the carbon content. This method is commonly used in South Africa to produce grades of refined (Medium and Low Carbon) Ferro-manganese with Mn 75%-80% and higher with varying carbon contents from 0.1% to 2%. The price of the alloys increases as the carbon content is reduced and unlike standard Ferro-manganese is usually sold per unit of manganese contained.
Mn : 70 - 75 %
C : 0.1% Max
P : 0.35% Max
S : 0.35% Max
Si : 1.5%
Size : 20 - 150 mm
​
Medium Carbon Ferromanganese:
When liquid Silicomanganese is reacted with Manganese Ore or a high MnO rich slag, the silicon is oxidized increasing the Mn content of the alloy without an increase in the carbon content. This method is commonly used in South Africa to produce grades of refined (Medium and Low Carbon) Ferro-manganese with Mn 75%-80% and higher with varying carbon contents from 0.1% to 2%. The price of the alloys increases as the carbon content is reduced and unlike standard Ferromanganese is usually sold per unit of manganese contained.
​
Mn : 70 - 75 %
C : 1 - 2% Max
P : 0.35% Max
S : 0.35% Max
Si : 3 - 4 %
Size : 20 - 150 mm
​
High Carbon Ferromanganese:
Chemical Analysis
Mn : 70 - 75 %
C : 6 - 8% Max
P : 0.35% Max
S : 0.35% Max
Si :3 - 4 %
Size : 20 - 150 mm
FERRO-TITANIAM

Ferro-titanium is used by stainless steel makers as a stabilizer to prevent chromium carbide from forming at grain boundaries and in the production of low carbon steels for sheet production.
Ferro-titanium is manufactured by melting titanium scrap (sponge, chips and solids) with iron in an induction furnace.
We have an extensive scrap processing operation to identify and control titanium scrap. All raw material is analytically tested by an independent assayer before dispatch to the production plant. The ingot is tested and then verified after crushing to ensure accuracy of analysis.
Packing:​
-
1mt bags
-
To your specification
​
Available Size:​
-
0-2mm
-
2-10mm
-
5-30mm
-
10-50mm
​
Chemical Property
Material Standard Specification​
-
Ti : 30% to 35% (Approx)
-
Si : 2% to 4% (Approx)
-
C : 1.5% max. (Approx)
-
S : 0.04% (Approx)
-
P : 0.03% (Approx)
-
Al : 6% (Approx)
FERRO-TUNGSTEN
.jpg)
Ferro-tungsten is an alloy, which is formed by combining iron and tungsten with a tungsten content range in two grades (A and B) and the content ranges are 75%-82% and 70%-75% respectively. Ferro-tungsten is a remarkably robust alloy because of its high melting point, tungsten has the second-highest melting point after carbon. By combining iron with tungsten, the tendencies towards brittleness are overcome from the raw state of tungsten, and Ferro-tungsten is often a major component of popular superalloys.
Uses of Ferro-tungsten:
A good example of Ferro-tungsten usage is in high-speed steel, which may contain as much as 18% pure tungsten. These superalloys that employ Ferro-Tungsten are used in the production of turbine blades and other wear-resistant coatings and parts. Other applications requiring the high density of Ferro-Tungsten alloys are heat sinks, counterweights, ballast keels, commercial aircraft tail ballast, and NASCAR and Formula 1 car ballast. In armaments, Ferro-tungsten is used in kinetic energy penetrators as an alternative to depleted uranium, but is also used in projectiles and grenades to create supersonic shrapnel. Ferro-tungsten is also used in the manufacture of game darts for the popular bar game (the Ferro-tungsten creates darts yielding smaller diameters, thus tighter groupings during play). Ferro-tungsten is also found in fishing lures (as the Ferro-tungsten alloy beads sink rapidly).
​
Properties of Ferro-tungsten​:
Ferro-tungsten as an additive to the production process of ferrous metals will impart several desirable properties upon the new alloy. One of the primary benefits of adding Ferro-tungsten to an alloy is to increase the alloy's melting point, making it suitable for aerospace applications as well as welding applications. Additionally, by adding Ferro-tungsten to an alloy, one can take advantage of tungsten's unique electrical capabilities as a conductor. For example, tungsten is used in field emission guns like electron microscopes and in IC chips, as well as metallic films that can replace conventional copper wiring.
​
Chemical Property
W: 77.53% (Approx)
As: 0.062% (Approx)
C: 0.100% (Approx)
Cu: 0.0745% (Approx)
S: 0.071% (Approx)
Sb: 0.037% (Approx)
P: 0.048% (Approx)
Sn: 0.049% (Approx)
Si: 0.40% (Approx)
Mn: 0.23% (Approx)
Pb: 0.003% (Approx
Size: 10-50 mm (Approx)
FERRO-SILICON MANGANESE
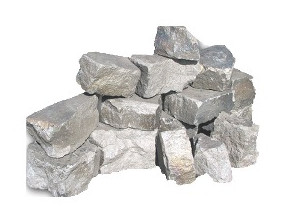
Ferro-silicomanganese is an alloy of manganese, silicon and iron. It is applied in metallurgy while in steel production for steel deoxidation and alloyage. ​
Silico-Manganese. Silico-Manganese is an alloy containing the high amount of manganese and silicon. This range of alloys is made by heating oxides MnO2 SiO2, Fe2O3 with carbon. It finds extensive applications as deoxidizer and an alloying element in steel
We are offering high quality Ferro-SilicoManganese For Industry These are available in the market at the most competitive prices. Ferro-SilicoManganese offered by us find wide application in iron and steel industries.
​
Specifications :​
-
Mn: 60% - 65% (Approx)
-
Si: 14% - 15% (Approx)
-
C: 2.00% Max (Approx)
-
P: 0.3% Max (Approx)
-
S: 0.03% Max (Approx)
FERRO-MOLYBDENUM

Ferro-Molybdenum prevents corrosion in stainless steel, and when mixed with iron, the Molybdenum also strengthens and hardens into austenite. Ferro-Molybdenum is mainly produced by Alumino Thermit Process. Moly Oxide, which is the raw material is produced in Chile. Ferro-Molybdenum is produced in India, China, Iran & Europe
Ferro-Molybdenum applications:
Ferro Molybdenum is added to an alloy due to its hardening properties that make steel extremely strong and at the same time weldable. Ferro Molybdenum also helps in increasing Corrosion resistance. The largest practical applications of Ferro Molybdenum are its use in ferrous alloys, and depending on the molybdenum content range, it is suited for machine tools and equipment, military hardware, refinery tubing, load-bearing parts and rotary drills. Ferro-Molybdenum is also used in cars, trucks, locomotives and ships. In addition, Ferro Molybdenum is used in stainless and heat-resisting steels that are employed by synthetic fuel and chemical plants, heat exchangers, power generators, oil-refining equipment, pumps, turbine tubing, ship propellers, plastics and inside acid storage containers.
Tool steels, with a high percentage range of Ferro-Molybdenum, are used in high-speed machining parts, cold work tools, drill bits, screwdrivers, dies, chisels, heavy castings, ball, and rolling mill.
​
Uses of Ferro-Molybdenum​:
The largest practical applications of Ferro-molybdenum are its use in ferrous alloys, and depending on the molybdenum content range, it is suited for machine tools and equipment, military hardware, refinery tubing, load-bearing parts and rotary drills. Ferro-molybdenum is also used in cars, trucks, locomotives and ships. In addition, Ferro-molybdenum is used in stainless and heat-resisting steels that are employed by synthetic fuel and chemical plants, heat exchangers, power generators, oil-refining equipment, pumps, turbine tubing, ship propellers, plastics and inside acid storage containers. Tool steels, with a high percentage range of Ferro-molybdenum, are used in high-speed machining parts, cold work tools, drill bits, screwdrivers, dies, chisels, heavy castings, ball and rolling mills, rolls, cylinder blocks, piston rings and large drill bits.
​
Specifications: